When it comes to modern automation, the type of motor you choose plays a huge role in the efficiency, accuracy, and longevity of your system. Whether you’re building an industrial robot, a conveyor system, or a high-precision CNC machine, two names always stand out — Servo Motors and DC Motors. But which one truly drives smarter automation? Let’s walk through the differences in a simple, human-friendly way to help you decide.
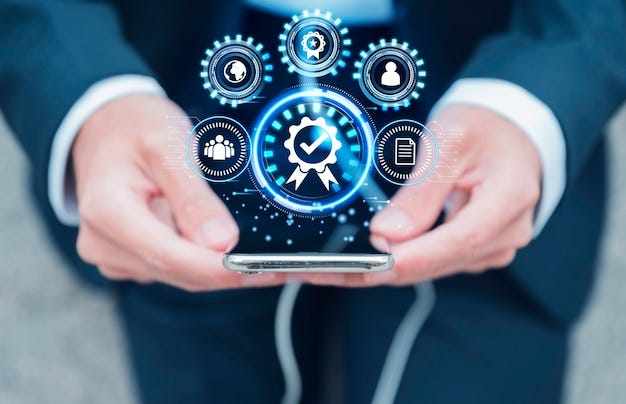
DC motors, short for Direct Current motors, are the classic workhorses of the industrial world. Known for their simplicity and reliability, they convert direct electrical current into mechanical rotation. Their speed can be controlled easily by adjusting voltage, and they’re widely used in applications like conveyor belts, pumps, fans, and even electric vehicles. The straightforward design of DC motors makes them easy to install and cost-effective, especially when your project doesn’t require ultra-precise motion. However, they do lack feedback mechanisms, which means the motor spins at a set rate depending on the voltage supplied — there’s no self-correction if the speed or position drifts.
On the other hand, Servo Motors bring precision and intelligence to the table. Unlike DC motors, servo systems are equipped with sensors, usually encoders, that continuously send feedback to the control unit. This closed-loop system allows servo motors to self-correct and maintain accurate positions and speeds even when the load changes, making them perfect for tasks like robotic arms, automated assembly lines, camera systems, and CNC machinery. If your project demands pinpoint accuracy and dynamic response to real-world conditions, servo motors are often the smarter pick.
Another key difference lies in torque and speed performance. DC motors are known for their high starting torque, which is a big advantage if you’re lifting heavy loads or running systems like hoists or elevators. However, they tend to lose torque consistency as the speed increases. Servo motors, in contrast, offer stable torque across a wide range of speeds, making them a great choice for applications where both strength and precision are non-negotiable. Whether you’re running a fast-moving robot or an automated packaging line, a servo motor can handle the variations in speed and load with impressive stability.
Durability and maintenance are other important factors when choosing between these two motor types. DC motors generally require more hands-on care because of their brushes, which wear out over time and need replacing to avoid breakdowns. Servo motors, especially brushless models, are designed to last longer with minimal maintenance. The absence of brushes not only reduces wear and tear but also makes them quieter and cleaner to operate. For industries where uptime is crucial and maintenance downtime is costly, servo motors often offer better long-term value.
Of course, cost is always a deciding factor for any project. DC motors usually have a lower upfront price tag and are easier to set up, making them ideal for small-scale projects or when the budget is tight. Servo motors do come with a higher initial cost, largely due to their integrated feedback systems and superior control capabilities. But when you factor in lower maintenance, longer lifespan, and higher performance, servo motors often justify their price, especially for complex or precision-driven automation systems.
Energy efficiency is yet another area where servo motors pull ahead. Thanks to their closed-loop feedback systems, servo motors optimize their power usage based on real-time needs. This not only minimizes energy waste but can also lead to noticeable savings on electricity bills over time. DC motors, lacking such real-time adjustments, tend to draw more power even when it’s not necessary, which can push up operational costs, especially in systems that run continuously.
And if you’re thinking about long-term scalability and smart automation, servo motors integrate effortlessly with modern digital control systems, IoT platforms, and even AI-driven monitoring tools. They’re designed for industries looking to future-proof their equipment and take advantage of Industry 4.0 innovations. While DC motors can be reliable and practical for standalone systems, they aren’t built with the same level of smart technology compatibility.
So, when you really think about it, the question isn’t which motor is better — it’s about which motor is right for your specific needs. If you’re working on a simple, budget-conscious project that doesn’t demand high precision, a DC motor is likely all you need. But if you want smarter automation — the kind that runs smoothly, self-corrects, saves energy, and can easily scale with your future tech — then a servo motor is worth the investment.
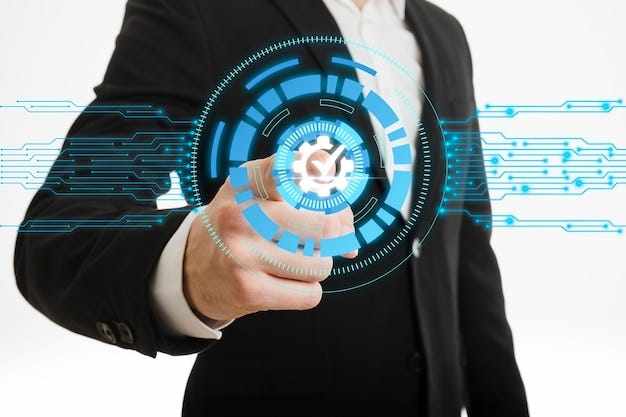
Choosing the right motor is about balancing your budget, performance goals, and long-term plans. Both DC and servo motors have their place in the world of automation, but the smarter choice comes down to understanding what your system really demands. If your goal is accuracy, adaptability, and energy efficiency, servo motors clearly drive smarter automation. If your goal is simplicity and upfront savings, DC motors can still be your go-to. The bottom line is: think long-term, calculate the total cost of ownership, and you’ll make the choice that pays off.
Write a comment ...